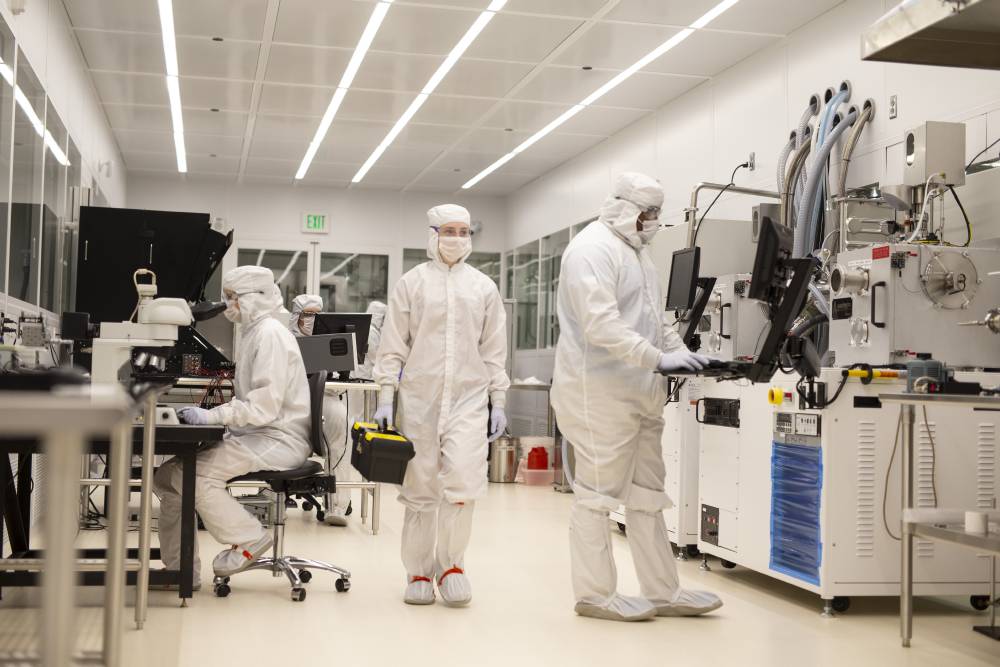
Equipment Categories
- Electron Beam Lithography System - Raith eLiNE
- Photoplotter - Bungard Filmstar-PLUS Small
- Laser Writer - Heidelberg Instruments μPG 101
- Layout Editor Software - Tanner L-Edit
- Mask Aligner - Karl Suss MA-6
- Assorted spin coaters and hot plates
- Atomic Layer Deposition - PicoSun R-200 Advanced
- Electroplating System
- Plasma-Enhanced Chemical Vapor Deposition - Trion Orion II with Triode Upgrade
- Multimode Deposition - Angstrom Amod - Combined E-beam, Resistive & Sputter Deposition Chamber
- Resistive Evaporator - Angstrom Amod - Resistive Chamber
- Sputter Deposition - AJA ATC-2200
- Tube Furnace - Lindberg Blue M Mini-Mite (1" diameter)
- Tube Furnace - MTI OTF-1200X (4" diameter)
- Deep Reactive Ion Etch - Oxford PlasmaPro 100 Cobra ICP-RIE
- Microwave Plasma Asher - PVA TePla IoN Wave 10
- Reactive Ion Etch Chlorine - Trion Minilock II RIE
- Reactive Ion Etch Fluorine - Trion Phantom II ICP-RIE
- Plasma Cleaner - Harrick Plasma PDC-32G
- Porous Silicon Etching System - AMMT MPSB 100
- XeF2Vapor Etch - SPTS Xactix e2
- HMDS Oven - Yield Engineering Systems 310TA
- Vacuum Oven - Thermo Scientific Lindberg Blue M VO Series
- Standard Oven - Thermo Scientific Heratherm OGS60
- Standard Oven - Yamato Drying Oven DX 300
- Cleanroom Glovebox - Inert PureLab HE connected to Angstrom Amod deposition chambers
- Microfluidic Flow Control System - Fluigent LineUp Series
- Rapid Thermal Processor - SSI Solaris 150
- Process Hoods - Acid/Base, Develop, EBL, HF, Liftoff, Microfluidics (SU-8), Photoresist, RCA Clean
- Dicing Saw - Disco DAD3220
- Wire Bonder - Westbond 7476D Wedge
- Contact Angle Goniometer - Ossila L2004A1
- Four Point Probe - Ossila T2001A
- Probe Station - Micromanipulator 450PM, Keithley 4200A-SCS
- Solar Testing - Oriel Instruments 100W Xenon Lamp with AM 1.5G filter, Cornerstone 130 Monochromator, Keithley 2400 SMU
- Stylus Profilometer - KLA Tencor P-7
- Assorted optical microscopes for inspection and digital imaging
- PDMS Aligner - ThorLabs motion control, DinoLite Optics
- Screen Printer - MTI EQ-SPC-2-LD
User Fees
Facility Details
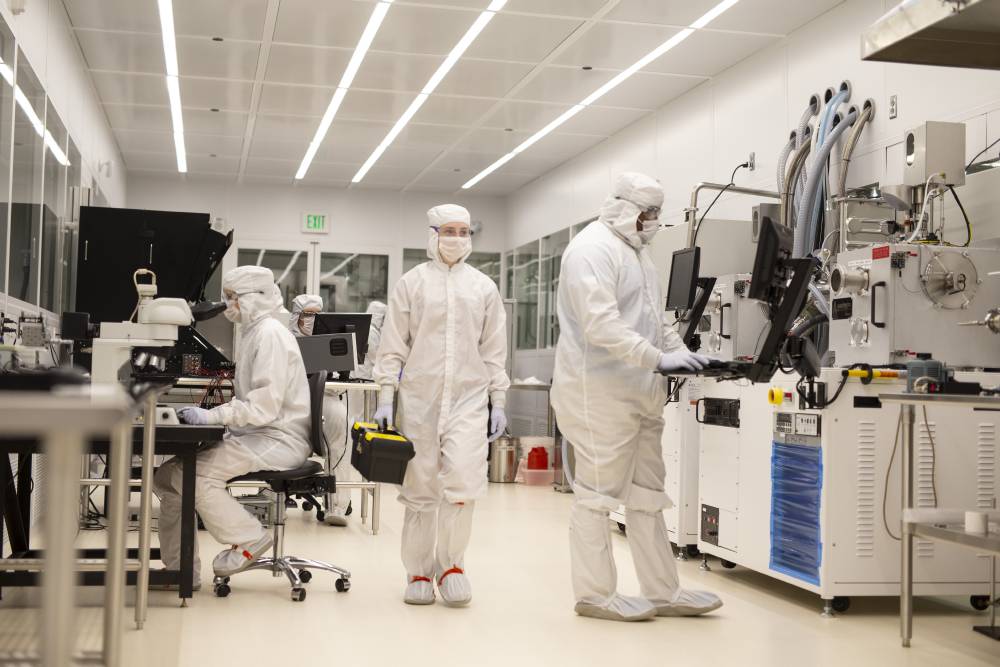
-
✓
30+ Fabrication and Characterization Tools
-
✓
10,000 Square Foot Facility
-
✓
Class 100/1000
-
✓
Material Deposition and Etch
-
✓
Lithography and Mask Making
-
✓
Processing and Packaging
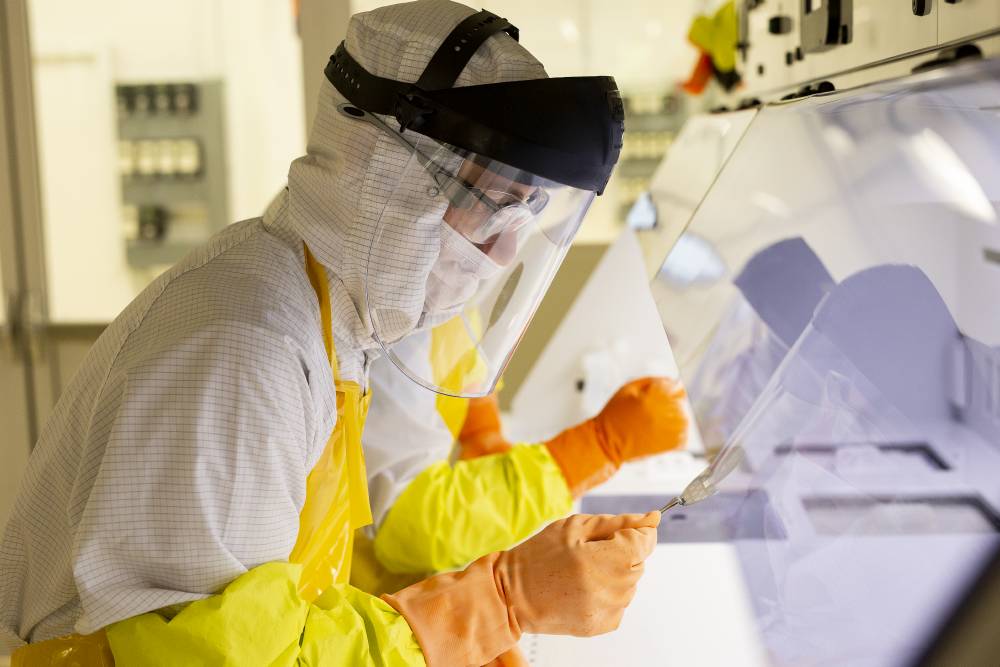
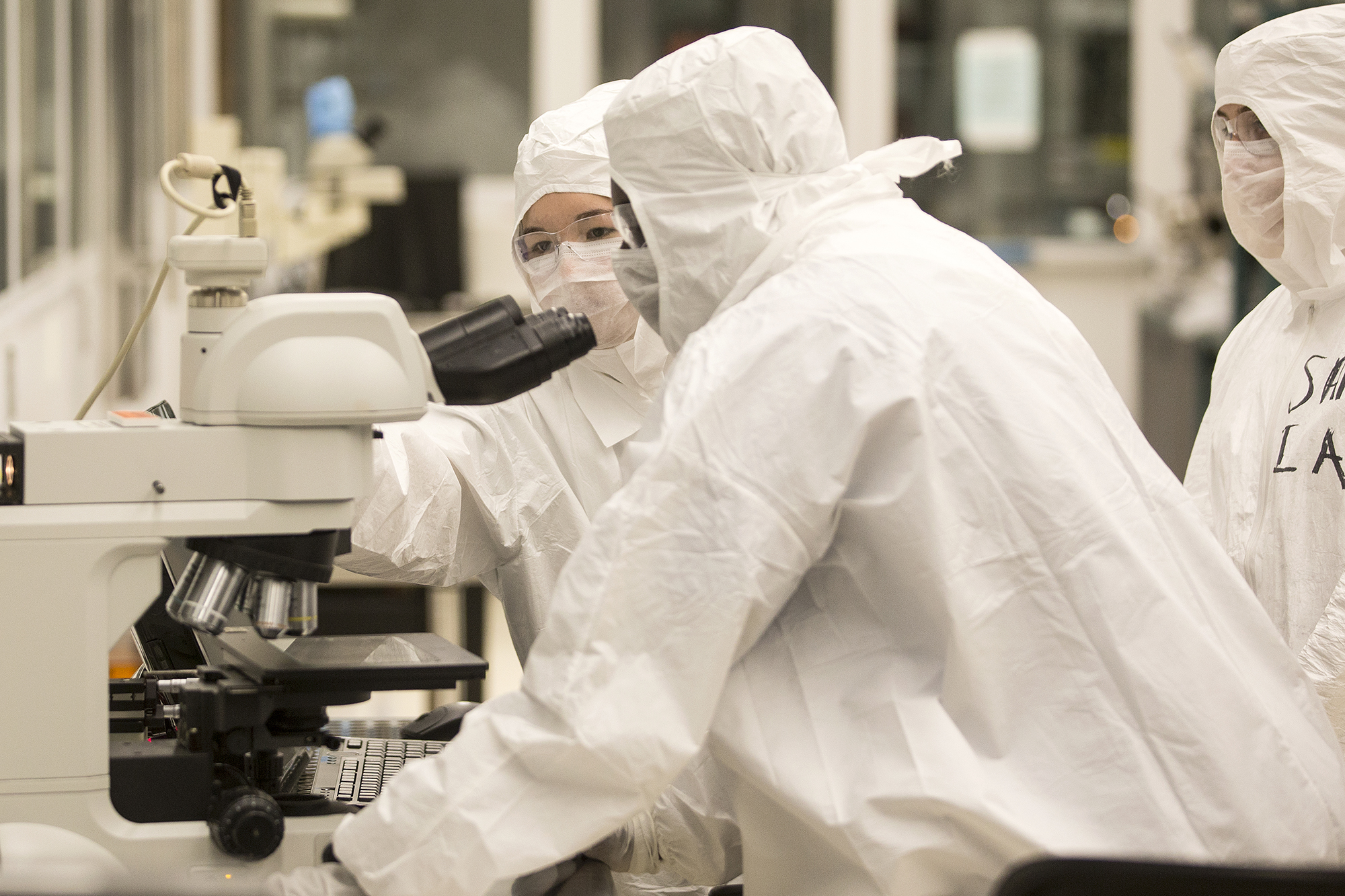
Processing Bays
There are two ISO 5 (Class 100) lithography bays with a combined area of 1100 ft2 plus a separate 250 ft2 ISO 6 (Class 1000) e-beam lithography (EBL) enclosure designed to noise criterion (NC) 25.
Two additional ISO 6 (Class 1000) bays totaling 1400 ft2 are utilized for deposition, etch and metrology activities.
Temperature and Humidity
Air temperature and moisture levels are controlled at at 68 +/- 2 C and 44 +/- 4 C relative humidity (RH), respectively, via a cleanroom-dedicated make-up air system. Central utilities for house and high-purity nitrogen, compressed dry air (CDA), process vacuum, process cooling water and type E-1 ASTM electronics and semiconductor grade water are provided along with solvent and corrosive exhaust systems that utilize point-of-use (POU) scrubbers for specialty gases.
Space Specs
The bay and chase design of the cleanroom totals approximately 10,000 sqft of floor space. The cleanroom has been designed with flexibility for adding future equipment and expanding and/or reconfiguring floor space including an area for converting 500 ft of chase area into a fifth processing bay.
Located on the main floor of the Vanderbilt ESB with floor-to-ceiling windows, the VINSE cleanroom design provides a safe and unique viewing experience for tours, outreach groups and casual observers from both inside and outside the building
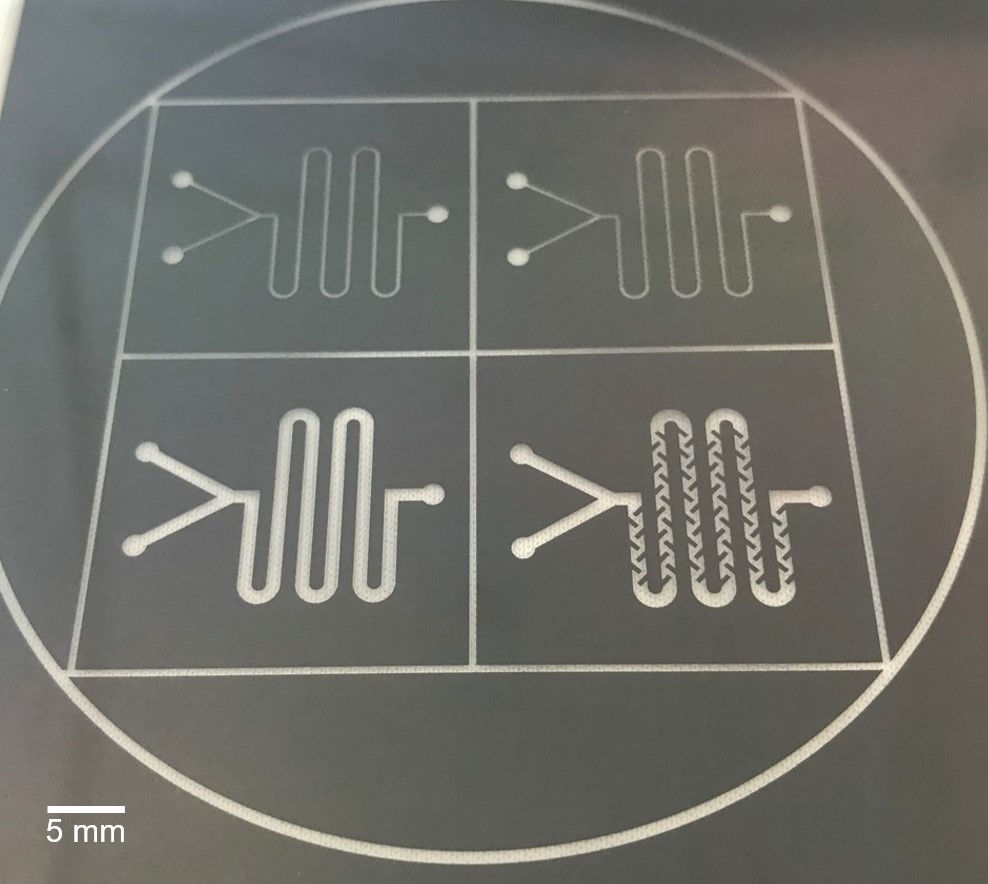
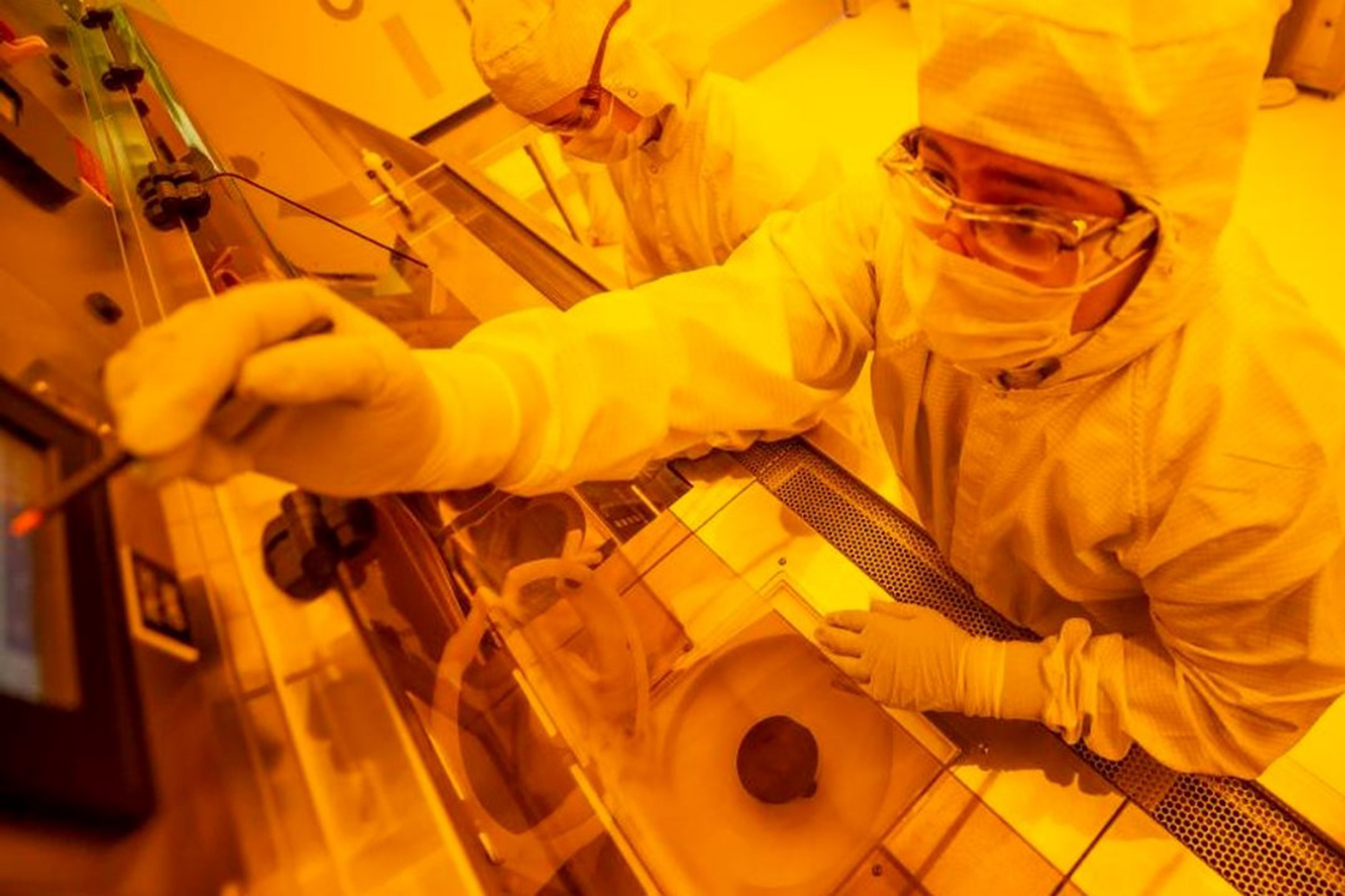