From French Fries to Clean Fuel: Using recycled vegetable oil, biodiesel inititative seeks to improve air quality on campus
[Originally published in The Vanderbilt Register]
By Kara Furlong
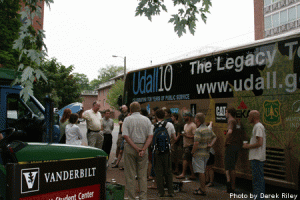
A Vanderbilt student group’s love of nature and desire to conserve natural resources has led to a project that will produce cleaner-burning fuel for use on campus.
The Vanderbilt Biodiesel Initiative, started by participants of Vanderbilt’s Wilskills program, will take used vegetable oil – the stuff that cooks French fries and other fried foods in campus cafeterias – and recycle it into environmentally friendly biodiesel.
Wilskills is an outdoor education program that uses rock climbing, caving, hiking and white water canoeing to teach wilderness skills. The program operates a six-day orientation experience on the Cumberland Plateau for incoming first-year students, as well as additional excursions throughout the year. “We have a van that we take out every weekend, and we were using a lot of gas,” said Derek Riley, a Wilskills instructor and graduate student in computer science. “We’re an environmentally responsible group, we like to think, so we thought we’d look into using biodiesel.”
Biodiesel is a processed fuel derived from biological sources that can be used in unmodified diesel-engine vehicles. Vegetable oil can be used in any diesel engine that has been converted to burn it, “but you have to pay for the conversion,” Riley said. “With biodiesel, if you convert the vegetable oil first, you can use it in any diesel vehicle.”
Enlisting the help of other campus groups, such as Vanderbilt’s Outdoor Recreation Program and the student recycling group SPEAR, proponents of a campus biodiesel initiative set out to acquire processing equipment. Unable to find a commercial product that was affordable and would produce biodiesel to its standards and in the quantities it desired, the Vanderbilt group tapped into its in-house expertise.
“We have a couple of chemical engineers involved, lots of engineering students, just lots of creative people in general,” said Riley, who cites Professor of Civil and Environmental Engineering Jim Clarke as a chief adviser. “We talked about ideas and came up with a design, which we continued to work on and refine. I’m sure the final design will take a bit of tweaking yet.” From the design the group built a working pilot system that can produce 50 gallons of biodiesel in a batch.
Riley explained how the process works: The idea is to make the vegetable oil thinner, so that it will burn at the same temperature as regular diesel. This is done through a chemical process called transesterification. “You combine the vegetable oil with methanol and lye, or in our case, instead of using lye – sodium hydroxide – we’re using potassium hydroxide,” he said. “Essentially you combine these three ingredients and mix them up, and the biodiesel floats to the top while glycerol settles on the bottom.”
At this point, the product is usable biodiesel, though its pH is a bit high. “So we go through another step called washing,” Riley said. “We’re using a unique washing technique that uses a product called Magnesol – it’s essentially synthetic talc powder – that doesn’t require water, so it’s an environmentally friendly step as well.”
The glycerol byproduct from the first part of the process can be used to make soap products, cosmetics, protein supplements for animals, even fertilizers. Vanderbilt’s current efforts to recycle vegetable oil from its cafeterias result in these products. “But in all of those cases, there are trucks coming in and picking it up and driving it to a processing facility somewhere out of state,” Riley said. “Our plan is to keep the oil here, convert it and use it right on campus.”
Campus-produced biodiesel will be used in Plant Operations equipment and possibly in medical center shuttle buses. The Wilskills program has purchased a diesel-engine van that will run on 100 percent biodiesel.
“The project is going to reduce the amount of fuel consumed on campus in significant ways,” Riley said. “It’s going to increase awareness about biodiesel and biofuels, and it’s going to reduce emissions.” Biodiesel produces about 60 percent less net carbon dioxide emissions than petroleum-based diesel. It also is a better lubricant, cleansing the engine and removing deposits in the fuel lines, meaning less wear on the engine over time.
Once the biodiesel group receives the necessary permits from Metro government ensuring that its project meets air-quality regulations, it will use the design of its pilot system – currently located at Riley’s house – to construct a 125-gallon system to be housed at Vanderbilt’s Power Plant. They hope to have the campus system up and running around Sept. 1.
Initial plans call for the group to provide 50 gallons of biodiesel to Plant Operations per week, “but when we can provide more, they said they will use more,” Riley said. “Once we’re established, we’d like to double the system’s size and add a second 125-gallon system. We’d be able to run them in parallel and actually produce 250 gallons at a time.
“I think there’s enough oil supply on campus that we eventually could be converting 500 to 600 gallons a week into biodiesel. Down the road, we’re looking at potentially making 2,000 gallons of biodiesel a month, which is pretty significant for a student-run project.”
Beginning this fall, students involved in the Wilskills program will collect vegetable oil from Rand Dining Hall and The Commons’ new dining facility as part of regular stops along their recycling routes. The biodiesel group is in talks with Vanderbilt Medical Center to receive waste oil from its cafeterias as well.
Though the processing system will initially run on electricity, future goals include powering it with a biodiesel generator or through solar power. “The original idea was to do it completely off the grid, using no water, no electricity – but we’re going to start out simple and add green components as we go,” Riley said.
Riley said that he and other organizers were surprised by the level of interest on campus in biodiesel. Volunteers involved with the group include undergraduate and graduate students, faculty and staff from all walks of the university and medical center.
The group’s ideas were solidified by its involvement this spring in MTV-U’s Ecomagination Challenge, a national competition that called for university teams to submit proposals for campus-based environmental initiatives. Among more than 100 entries, Vanderbilt’s project was a top 10 finalist. Though the group didn’t win the $25,000 grand prize, the experience was invaluable. “It helped us focus what our goals were, to get everything down on paper. It helped us get organized and it raised the level of consciousness for the project on campus,” Riley said.
With the support of Vanderbilt’s administration and help from officials in Plant Operations and Environmental Health and Safety, the Vanderbilt Biodiesel Initiative is pressing forward with the conviction that the time and setting for its project couldn’t be more right.
“Biodiesel is a really good fuel,” Riley said. “The problem is it’s a little dirty to collect, so it’s not something that’s being adopted everywhere. But I think it’s ideal for a student group to get involved with.”
And there’s no mistaking clean-burning biodiesel for the other fuels out there, according to Riley.
“When you use biodiesel, the exhaust smells like fried food. It’s a funny byproduct. When we were doing our initial tests, the guys in Plant Ops who were using the biodiesel actually complained about it – they said they preferred the diesel smell. It’s definitely something you have to get used to.”
Leave a Response